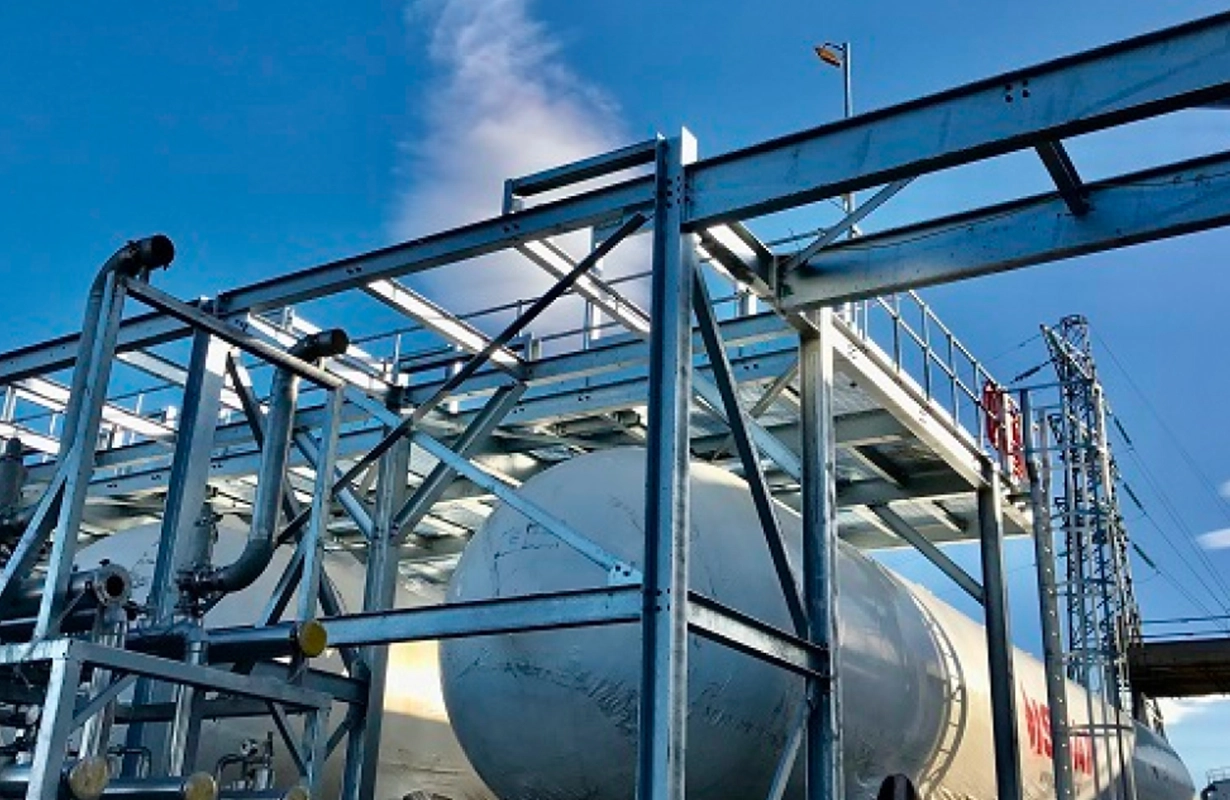
The next step to Net Zero
Our CCU plant will be capable of capturing and producing up to 40,000 tonnes of carbon dioxide per year (equivalent to taking 20,000 cars off the road) and will reduce our carbon emissions at the CHP plant by over 10%.
A world first
Carbon dioxide captured from energy generation emissions is then purified to food and pharmaceutical grade for use as a raw material in the manufacture of sodium bicarbonate, which will be known as EcoKarb® and will be exported to over 60 countries around the world. Much of the sodium bicarbonate exported will be used in haemodialysis to treat people living with kidney disease.
A UK first
The CCU is the first of its kind and the largest in the UK and was designed and delivered alongside Pentair, a leading supplier of carbon dioxide capture and purification technologies. This plant is an important step in decarbonising industrial activity and was even invested in by the UK government to support their target of Net Zero carbon emissions by 2050.
Since operations started in summer 2021, the CCU has significantly reduced Tata Chemicals Europe's carbon emissions, whilst also securing a sustainable supply of carbon dioxide – a key raw material critical to our business’s international growth.
Global growth
Not only will the CCU plant reduce carbon emissions from our Combined Heat and Power plant (CHP), making it one of the most carbon efficient power plants in the UK, the project will be a springboard for Tata Chemicals Europe to unlock further growth into our export markets. Global demand for high grade sodium bicarbonate is growing as more of the world’s population has access to healthcare, and Tata Chemicals Europe already exports 60% of its sodium bicarbonate to more than 60 countries across the globe.
Patented technology
In a unique and patented process, the CCU plant will capture carbon dioxide from the flue gases of our 400MW heat, 96MW electricity gas-fired, combined heat and power plant, which supplies steam and power to our company’s Northwich operations and other industrial businesses in the area.
How does it work?
The CCU plant will then purify and liquify the gas which will then be stored ready for use in the manufacture of sodium bicarbonate, to be called EcoKarb®. Deploying CCU technology will reduce emissions, as captured carbon dioxide will be used in the manufacturing process rather than being emitted into the atmosphere.
Reducing emissions
Already one of the most efficient power plants in the UK, our CHP plant is a low-carbon source of electricity, currently producing half the amount of carbon dioxide per kWh of electricity generated compared to a typical gas fired power station. The new CCU plant has reduced the carbon dioxide per kWh electricity generated even further, reducing the carbon intensity of our soda ash and sodium bicarbonate products and sets a new benchmark for the industry.
Investing in future
Another move that will play a major part in reducing the company’s carbon footprint this year is our £8m investment in state-of-the-art boilers and associated infrastructure at British Salt in Middlewich – for more information about this project, please see here.
Our journey to Net Zero
The CCU is just one of the many ways we are working towards a Net Zero future. If you want to know more about how we’re working towards a greener future, then check out our sustainability brochure.